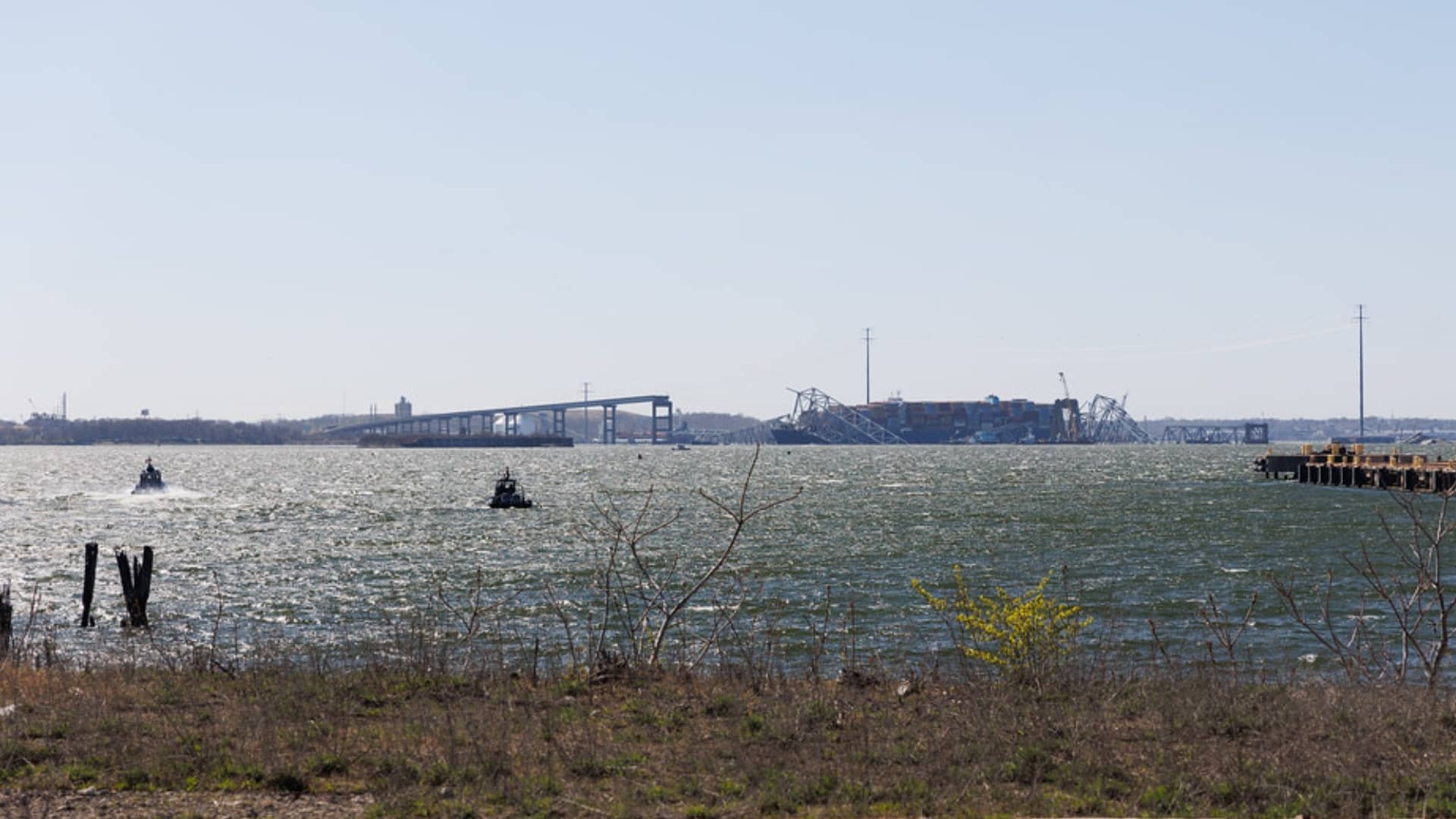
Supply Chain Impacts of the Baltimore Bridge Collapse
Despite the challenges posed by the Francis Scott Key Bridge collapse on March 26, the Port of Baltimore has demonstrated remarkable resilience. Authorities have opened a small channel, allowing limited shipping at the port for the first time since the disaster. While rebuilding the bridge could take 18 months to several years, the port’s ability to adapt and continue operations is a testament to its unwavering reliability in the U.S. supply chain.
The Port of Baltimore typically ranks among the top ports in the United States regarding cargo volume. The port handles significant total tonnage, particularly for automobiles, coal, and containerized goods. This high cargo volume underscores the port’s importance as a vital link in the supply chain, facilitating the movement of goods domestically and internationally.
Meanwhile, goods still must continue moving. The ports in Baltimore, particularly the Port of Baltimore, play a significant role in the U.S. supply chain. Here is why:
Strategic Location
Baltimore’s ports are strategically located along the East Coast of the U.S., making them key entry and exit points for goods destined for the Mid-Atlantic region and beyond. The Port of Baltimore’s proximity to major population centers in the Northeast corridor and its access to major transportation networks, including railways and highways, make it a crucial hub for distributing goods throughout the region and beyond.
Economic Impact
Baltimore’s ports, particularly the Port of Baltimore, are crucial players in the U.S. supply chain and integral parts of local, regional, and national economies. They support thousands of jobs directly and indirectly in transportation, logistics, manufacturing, and retail. The economic activity generated by port operations, including cargo handling, warehousing, and distribution, contributes to the region’s overall prosperity and enhances its competitiveness in global markets, fostering a sense of shared prosperity.
Intermodal Connectivity
The Port of Baltimore offers excellent intermodal connectivity, with on-dock rail facilities and access to major interstate highways. This multimodal transportation infrastructure enhances the port’s efficiency and facilitates the seamless movement of goods between maritime, rail, and trucking networks. It also enables businesses to leverage multiple transportation modes to optimize their supply chain logistics and reduce transit times and costs.
Baltimore’s ports, particularly the Port of Baltimore, are integral to the U.S. supply chain, providing critical infrastructure and services supporting domestic and international trade. The ports collectively underscore their importance in facilitating the movement of goods and sustaining the competitiveness of businesses in an increasingly interconnected global economy.
Navigating the Aftermath
The reverberations are being felt far beyond Baltimore’s immediate vicinity. As a result, your supply chains face significant short-term and long-term challenges. This event serves as a stark reminder of the vulnerability of our infrastructure and the interconnectedness of global trade.
Among the repercussions and potential paths forward for businesses and stakeholders:
Short-Term Impacts
• Disruption in Transportation Routes – The collapse has severed a crucial artery in the transportation network, leading to immediate disruptions in the movement of goods. For instance, the closure of the Francis Scott Key Bridge has forced trucks to take longer routes, increasing transit times and fuel consumption. Roads and bridges are vital conduits for transporting goods, and any interruption can cause delays and bottlenecks.
• Supply Delays – Relying on just-in-time inventory management? You may face shortages as shipments are delayed or rerouted. This can lead to production slowdowns or stoppages, impacting revenue and customer satisfaction.
• Increased Costs – Rerouting shipments through alternative routes often incurs additional costs, such as higher transportation fees and increased fuel consumption. These added expenses can eat into your profit margins, particularly for businesses operating on tight budgets.
• Inventory Management Challenges – Maintaining optimal inventory levels becomes a precarious balancing act with supply chain disruptions. Excess inventory in transit or delayed deliveries can strain storage capacity and tie up working capital.
• Uncertainty and Risk – The sudden nature of the bridge collapse introduces uncertainty into supply chain planning. Your business may struggle to assess the full extent of the impact and devise contingency plans amidst evolving circumstances.
Long-Term Impacts
• Infrastructure Investment – The collapse underscores the pressing need for infrastructure investment and maintenance. Governments and stakeholders may prioritize infrastructure upgrades and inspections to prevent future incidents, potentially leading to long-term improvements in transportation networks.
• Supply Chain Resilience – The event serves as a wake-up call for you to reevaluate supply chain resilience strategies. Diversifying transportation routes, dual-sourcing critical components, and building redundancy into the supply chain become imperative to mitigate future disruptions.
• Regulatory Scrutiny – Regulatory agencies may intensify scrutiny and enforcement of infrastructure safety standards after the collapse. Compliance requirements could become more stringent, impacting your operating costs and operational practices.
• Insurance and Risk Management – In light of the bridge collapse, companies may reassess their insurance coverage and risk management strategies. Heightened awareness of infrastructure risks could prompt businesses to seek broader coverage or invest in proactive risk mitigation measures.
• Supply Chain Localization – Some businesses may explore supply chain localization strategies to reduce dependence on vulnerable transportation networks. Nearshoring or onshoring production facilities and sourcing materials locally can enhance resilience against external disruptions.
Navigating the Path Forward
Proactive measures are essential to mitigate short-term impacts and build resilience for the future in the face of supply chain disruptions precipitated by the Francis Scott Key Bridge collapse. Collaboration among stakeholders, including governments, businesses, and industry associations, is crucial to address infrastructure vulnerabilities and foster a more robust and adaptable supply chain ecosystem. This could involve sharing resources, information, and best practices to ensure a coordinated response.
Investing in technology and data analytics can enhance your supply chain visibility and agility, enabling rapid response to disruptions and optimization of transportation routes. Embracing sustainability initiatives can also align with resilience goals by promoting resource efficiency and reducing environmental risks.
The Baltimore bridge collapse poignantly reminds us of the interconnectedness of global supply chains and the imperative of proactive risk management. By learning from this event and embracing resilience-building measures, businesses can navigate the challenges posed by supply chain disruptions and emerge stronger and more adaptable in an ever-evolving landscape.
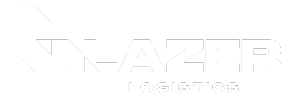
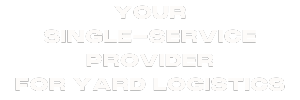
Lazer Logistics specializes in yard logistics solutions that optimize throughput at transition points across the supply chain.
Want a free
yard efficiency analysis?