Enhancing Ops Efficiency for a Beverage Company
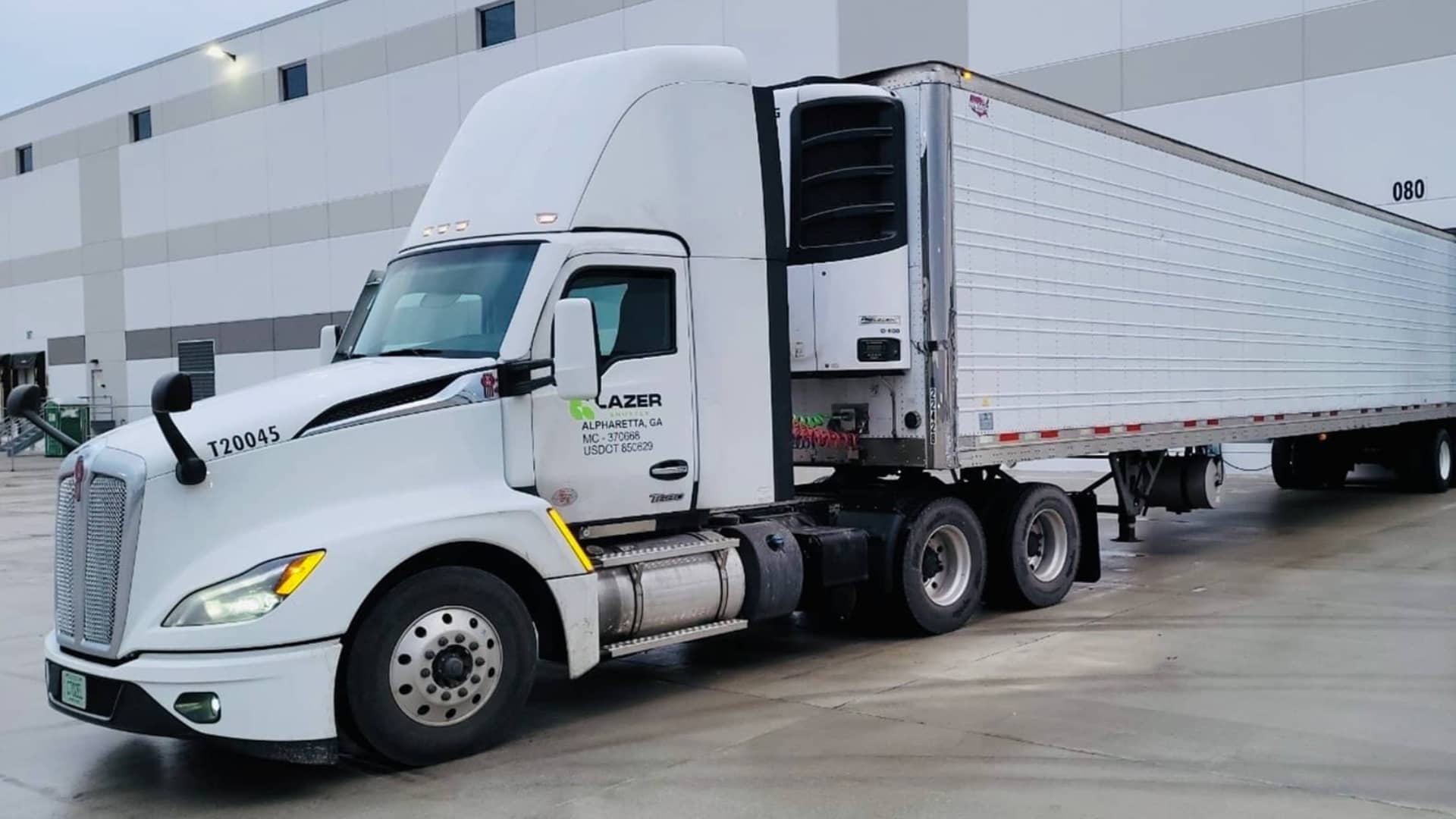
An beverage company partnered with Lazer Logistics to improve the efficiency and effectiveness of its yard management operations. The company was facing challenges with scheduling, production tracking, and overall visibility into key performance indicators (KPIs). Lazer Logistics, a leader in third-party logistics (3PL) services, was tasked with implementing solutions to address these issues.
Challenge
The beverage company needed a more dynamic and responsive yard management system to handle workload fluctuations. Their existing scheduling tools were rigid, making it difficult to staff effectively based on real-time demand. Additionally, the company struggled with tracking shuttle work accurately, which led to inefficiencies and a lack of transparency in production metrics.
Moreover, the company’s production reports were split across different operations sections, leading to incomplete data feeding into their KPIs. This fragmentation skewed the metrics and made it difficult for the operations team to get a holistic view of the yard’s performance.
Solution
Lazer Logistics implemented several critical solutions to address the beverage company’s challenges:
Dynamic Scheduling Tool
Lazer Logistics introduced a dynamic scheduling tool that allowed the company to better predict and manage its staffing needs based on projected workloads. This tool provided the flexibility required to adjust schedules in real-time, ensuring that the yard was always appropriately staffed, leading to improved efficiency and reduced labor costs.
New Job Code for Shuttle Work
Lazer Logistics created a new job code specifically for this purpose to address the tracking of shuttle work. This addition allowed the company to track dedicated shuttle work more accurately, adding transparency and control over their operations.
Production Trimming and KPI Alignment
Lazer Logistics restructured the production reporting system by correcting the split that was previously causing discrepancies in the KPIs. By ensuring that all production data fed correctly into the company’s KPIs, Lazer Logistics saved the beverage company three hours of administrative work in production entries. This change also added visibility into the total number of moves and miles per hour (MPH) averages, providing a more accurate and comprehensive view of the yard’s performance.
Results
The collaboration between Lazer Logistics and the beverage company led to significant improvements in operational efficiency:
Improved Staffing Efficiency
The dynamic scheduling tool enabled better staffing decisions, reducing overstaffing and understaffing, enhancing productivity, and reducing labor costs.
Enhanced Tracking of Shuttle Work
Introducing a dedicated job code for shuttle work allowed for more precise tracking, improving transparency and operational control.
Increased Visibility and Accurate KPIs
The correction in production reporting provided a more accurate reflection of the yard’s performance, saving time for operations and giving the company better insights into its operational efficiency.
Conclusion
This case study underlines Lazer Logistics’ ability to tailor solutions to specific customer needs, resulting in enhanced efficiency, better resource management, and more reliable performance metrics.
CONTACT US
Ready to learn more about how you can leverage our solutions to increase your throughput? Fill out this form, and a member of our team will contact you.